The Most Common Issues in Plasma Cleaning and Etching Systems
- Davide
- Aug 7, 2023
- 6 min read
Updated: Apr 25, 2024
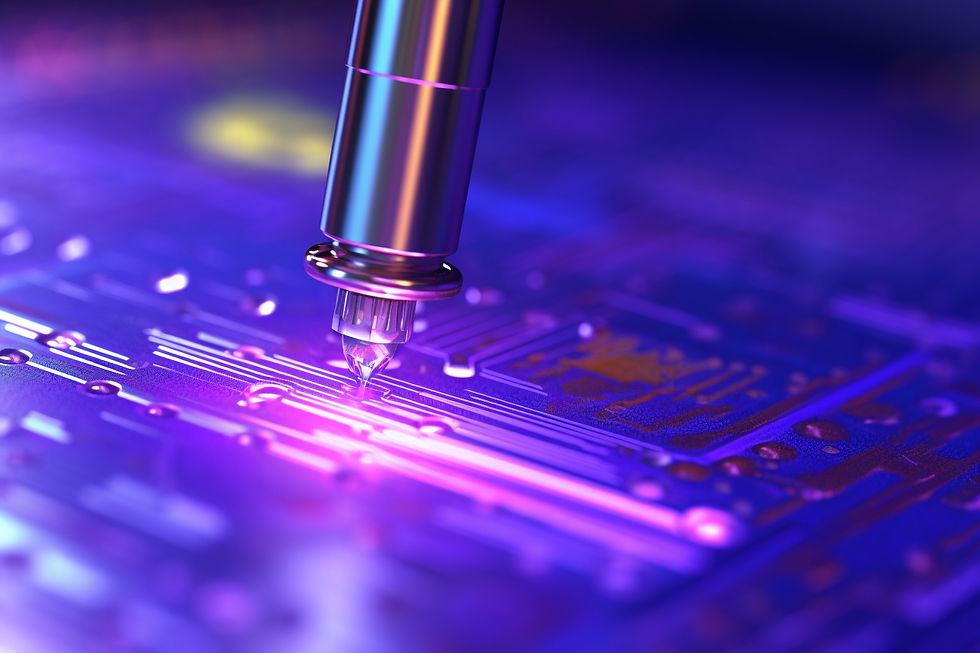
Plasma cleaning, a surface treatment technique utilized for the removal of contaminants and enhancement of material cleanliness, offers numerous advantages over traditional cleaning methods. However, like any process, plasma cleaning is not without its challenges.
Learn more about plasma cleaning
Addressing these challenges requires careful design, optimization of parameters, regular maintenance, and monitoring techniques. By understanding and overcoming these common issues, plasma cleaning can continue to serve as a valuable method for achieving high levels of cleanliness and surface preparation in industries such as microelectronics, optics, and medical device manufacturing.
With that said, we’ll explain all you need to know about the common issues in plasma cleaning and plasma etching systems in this article.
What Is Plasma Cleaning?
Plasma cleaning is a surface treatment technique that is used to remove contaminants and improve the cleanliness of various materials. It involves the use of low-temperature plasma, which is a partially ionized gas, to effectively clean surfaces.
The process of plasma cleaning begins by placing the object or material to be cleaned in a vacuum chamber. The chamber is then filled with a gas, such as oxygen, nitrogen, or argon. Next, an electric field is applied to the gas, which ionizes the gas particles, creating a plasma. The plasma contains a mixture of ions, electrons, and neutral species.
The ions and radicals present in the plasma have high kinetic energy, and they can react with the contaminants present on the surface of the material being cleaned. These contaminants can include organic residues, oils, grease, particles, oxides, and other types of impurities. When the ions and radicals collide with the contaminants, they break them down into smaller molecules or atoms. These smaller particles are then removed from the surface by various mechanisms such as desorption, sputtering, or volatilization.
Advantages of Plasma Cleaning
Plasma cleaning offers several advantages over traditional cleaning methods. Firstly, it can effectively clean surfaces at a microscopic level, reaching into crevices and removing even very small particles. It is also a dry cleaning method, which means it does not use liquid solvents that may leave residues or damage sensitive materials. Additionally, plasma cleaning can be a gentle process that does not harm the underlying substrate, making it suitable for delicate or sensitive materials.
Applications of plasma cleaning can be found in various industries. It is commonly used in electronics manufacturing, semiconductor fabrication, optics, medical device manufacturing, aerospace, and automotive industries. Plasma cleaning is particularly valuable in industries that require high levels of cleanliness and surface preparation, such as in the production of microelectronics, where even minute particles or contaminants can change the reliability of the devices.
Common Issues in Plasma Cleaning
These are the most common issues found in plasma cleaning.
Poor Plasma Uniformity
Poor plasma uniformity refers to a situation where the distribution of plasma across the surface being cleaned is uneven. In plasma cleaning, it is desirable to have a uniform plasma distribution to ensure consistent and effective cleaning of the entire surface. When there is poor plasma uniformity, certain areas may receive insufficient plasma exposure, leading to incomplete cleaning or inefficient removal of contaminants.
Addressing poor plasma uniformity requires a systematic approach involving careful design of the plasma chamber, optimization of gas flow and pressure, proper electrode configuration, and regular maintenance. Techniques such as magnetic fields, gas flow adjustments, and electrode modifications can be employed to improve plasma uniformity. Monitoring techniques, such as optical emission spectroscopy, can also be used to assess plasma uniformity and guide process adjustments.
Contamination Buildup
Contamination buildup in plasma cleaning refers to the accumulation of residues or by-products on the surfaces being cleaned or within the plasma chamber itself over time. Despite the effectiveness of plasma cleaning in removing contaminants, there are situations where certain residues can accumulate rather than being completely eliminated. This can impact the cleaning process and may require additional measures to mitigate or remove the buildup.
Contamination buildup can impact the efficacy of plasma cleaning by interfering with subsequent cleaning cycles, affecting process consistency, or compromising the quality of cleaned surfaces. It can result in reduced cleaning efficiency, increased surface roughness, altered material properties, or compromised device performance, particularly in industries that require high cleanliness standards, such as microelectronics or optics.
To mitigate contamination buildup in plasma cleaning, several measures can be taken, such as optimization of cleaning parameters, chamber cleaning and maintenance, use of additional cleaning techniques, and material selection.
Unwanted Sidewall Etching
Unwanted sidewall etching, also known as lateral etching or under-etching, is a phenomenon that can occur during plasma etching processes. It refers to the unintentional removal or erosion of material from the sidewalls of structures or features on a substrate, resulting in undesirable changes to the shape or dimensions of those features.
Unwanted sidewall etching can have negative consequences in various applications, especially in microelectronics, MEMS (Micro-Electro-Mechanical Systems), or semiconductor manufacturing, where precise control of feature dimensions and sidewall integrity is critical. It can cause changes in feature shape, dimensional variations, loss of material, or even structural instability.
To mitigate unwanted sidewall etching during plasma etching, several approaches can be considered, such as process optimization, gas chemistry selection, surface protection, process control, and continuous monitoring.
Process Drift and Instability
Process drift and instability in plasma cleaning refer to deviations or variations in the cleaning process parameters or performance over time. These deviations can result in inconsistent or unpredictable cleaning results, leading to reduced process efficiency, compromised cleaning quality, or even process failure.
There are several factors that can contribute to process drift and instability in plasma cleaning, for example, equipment ageing, contamination buildup (as previously discussed), gas purity and composition, and temperature variations.
Process drift and instability can have detrimental effects on the plasma cleaning process and the quality of the cleaned surfaces. These effects can include inconsistent removal of contaminants, variations in surface cleanliness, non-uniform plasma distribution, or reduced process repeatability.
To address process drift and instability in plasma cleaning, several key strategies can be employed, such as regular maintenance and cleaning, gas management and purification, process monitoring and feedback, process optimization, and standardization.
Different Types of Plasma Cleaning
There are different types of plasma cleaning, these are just a few:
Remote Plasma Cleaning (Downstream Plasma)
In remote plasma cleaning, the plasma is generated separately from the material being cleaned. The substrate or object is placed in a vacuum chamber, and the plasma is generated in a different region of the chamber. Reactive species, such as ions or radicals, are then transported to the surface of the substrate to remove contaminants through gas-phase reactions. This method is often used for delicate or temperature-sensitive materials.
Direct Plasma Cleaning
Direct plasma cleaning involves generating the plasma directly in contact with the surface being cleaned. The material to be cleaned is placed in the plasma chamber, and the plasma is generated in close proximity to the surface. The reactive species directly interact with the contaminants, leading to their removal. Direct plasma cleaning offers more efficient cleaning but may not be suitable for sensitive materials.
Microwave Plasma Cleaning
Microwave plasma cleaning utilizes microwave energy to generate the plasma. Microwaves are used to excite the gas molecules, leading to the formation of a plasma. This technique allows for precise control of plasma characteristics and can be used for various applications, including surface cleaning and surface modification.
Plasma Cleaning and SCI
In conclusion, plasma cleaning is a powerful surface treatment technique that offers numerous advantages in terms of cleanliness and contaminant removal. However, it is essential to address common issues such as poor plasma uniformity, contamination buildup, unwanted sidewall etching, and process drift and instability. By implementing appropriate measures and strategies, these challenges can be mitigated, ensuring consistent and effective plasma cleaning operations.
With continued advancements and improvements in plasma cleaning technology, industries can rely on this method to meet the high cleanliness standards required for various applications, from microelectronics to aerospace.
SCI Plasma stands as a highly esteemed organization, boasting a team of adept specialists who excel in providing top-notch plasma cleaning solutions. Leveraging their extensive knowledge and experience, they serve as invaluable partners for individuals and organizations seeking assistance in the realm of plasma cleaning.
Whether you seek clarification about the plasma cleaning process, require guidance in selecting the most suitable equipment, or demand tailored solutions for your unique cleaning needs, the experts at SCI Plasma are unwavering in their commitment to assisting you. Contact us today.
Comments