How Plasma Cleaning Improves Wire Bond Strength-and Why That Matters More Than You Think
- Davide
- 1 day ago
- 3 min read
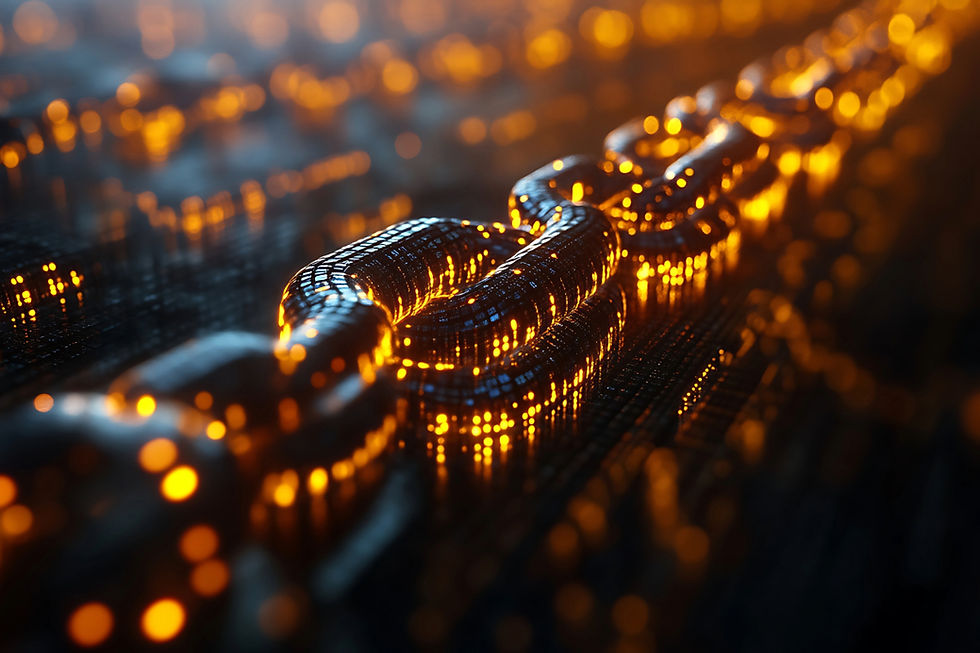
Wire bonding is a precision task—but strength and stability aren’t just about good machinery or skilled operators. They start with the surface itself.
If the substrate or lead frame isn’t clean at a microscopic level, bond strength becomes unreliable. Connections fail, signals degrade, and long-term stability suffers—especially under mechanical or thermal stress.
This is where plasma cleaning delivers real, measurable results. It ensures surfaces are not only free from contamination but are also chemically prepared to form stronger intermetallic bonds. Let’s look at how, and what changes when plasma is properly integrated into the pre-bonding process.
The True Test of Bond Strength
In wire bonding, there’s a simple but critical quality check: a mechanical pull test.
A small hook is used to pull the bonded wire until it breaks
The goal is to have the wire break on the wire itself, not at the connection point
If the bond fails before the wire does, you have a problem—weak bonding or surface contamination
When the bond is strong enough to outlast the wire, you’ve got a clean, reliable connection. And that’s not just good engineering—it’s peace of mind for every product that leaves your facility.
Surface Prep Determines Strength
Wire bonding isn’t just about physical contact—it’s about forming intermetallic compounds between the bond wire and the surface. These compounds form best when:
A. The surface is ultra-clean, with no residues from flux, solder, or previous process steps
B. The substrate is chemically activated to improve interaction at the atomic level
This is exactly what plasma cleaning delivers.
By removing molecular-level contaminants and energising the surface, plasma makes sure that the metal layers can fuse cleanly. The result? Stronger bonds. More stable connections. And far fewer surprises during pull tests or thermal cycling.
Getting the Parameters Right
Not all plasma cleaning is equal. Like any process, it needs to be tuned to the application.
• Most wire bonding applications use argon plasma, which is gentle but effective on metal surfaces
• The process depends on three main variables: power, pressure, and time
• These parameters must be optimised not just for cleaning—but also for bond performance
And here’s where the nuance comes in: you’re not just tuning the plasma. You’re tuning the plasma and the bonding process together.
That means working closely across departments or suppliers to ensure that the bond machine, the plasma tool, and the surface material are all aligned. It’s a systems-level approach—not just a surface tweak.
The Difference Over Time
It’s one thing to pass a pull test today. It’s another to survive five years of real-world conditions.
a) Vibrations from machinery
b) Temperature swings in the field
c) Long-term chemical exposure in automotive or aerospace environments
Plasma-treated surfaces form bonds that don’t just test better—they last longer. They’re less prone to corrosion, oxidation, and signal degradation. And they perform better across the full lifecycle of the component, not just the initial quality check.
In industries where reliability is tied to safety—automotive, aerospace, medical devices—that extra layer of assurance isn’t optional.
A Cleaner Bonding Process, A Stronger Business Case
The return on plasma cleaning is clear when it comes to bonding:
Stronger mechanical connections that pass destructive testing
Better electrical signal integrity and lower noise over time
Fewer failures due to contamination or inconsistent bond quality
Improved product qualification and reduced warranty risk
And let’s not forget: the cost of weak bonds isn’t just in failed units. It’s in delayed projects, strained supplier relationships, and reputational damage when parts don’t perform as expected.
Want to Strengthen Every Connection?
If your team is seeing inconsistent bond strength, failed pull tests, or long-term instability in wire-bonded parts, it’s worth taking a closer look at your surface prep process.
Plasma cleaning isn’t just about removing contamination—it’s about enabling stronger, longer-lasting bonds where they matter most.
Contact SCI Plasma to explore how plasma can help you create a cleaner, stronger, and more reliable bonding process.
コメント