Reactive Ion Etching (RIE) Explained in Simple Terms
- Davide
- May 25, 2023
- 4 min read
Updated: Aug 17, 2023
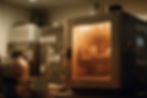
Reactive Ion Etching, abbreviated as RIE, is an intricate technique for removing microscopic amounts of material from a surface. It's an invaluable tool in manufacturing advanced components like semiconductors. Instead of leveraging liquid chemicals that dissolve the material, RIE employs a unique type of gas, plasma, which reacts with and disintegrates the material.
RIE's excellence lies in its precision. It's adept at creating accurate cuts and shapes because it etches primarily in a downward direction, limiting lateral movement. As a result, it's an essential technology in advanced industries that manufacture minute devices such as computer chips.
Consider the scenario where you're manufacturing the smallest computer chip in existence. The level of precision and accuracy required is extreme, to ensure flawless functionality. This is where RIE comes into play. Picture it as a precision instrument, akin to a microscopic laser beam capable of making incredibly precise cuts.
RIE represents a remarkable piece of technology, prevalent in some of the most technologically advanced industries. It plays a pivotal role in creating micro-devices with remarkable capabilities, such as powering your smartphone or operating a supercomputer.
In this article, we'll delve deeper into the workings of RIE, outline the difference between RIE and isotropic plasma etching, and discuss how consultation with experts at SCI Plasma can help you elevate your devices' performance and quality to new heights.
How Does Reactive Ion Etching Work?
The fundamental operation of Reactive Ion Etching is quite captivating. At its core, RIE is a type of dry etching technique that leverages chemically reactive plasma to remove material. This plasma is generated under low pressure (vacuum) by an electromagnetic field. High-energy ions from the plasma are directed towards the material, and the energy transfer causes the material's atoms to be ejected, essentially chipping it away bit by bit.
The process begins by placing the substrate - the material to be etched - in an etching chamber. A chemically reactive gas, often containing elements like fluorine or chlorine, is introduced into the chamber. The gas is then ionized into plasma, typically by applying radio frequency (RF) power, which creates an electric field within the chamber. This electric field accelerates the ions towards the substrate with a great deal of energy. When these energetic ions strike the substrate's surface, they react chemically with it. This reaction produces volatile by-products which are subsequently removed by vacuum pumping.
The degree of precision in RIE comes from controlling the direction of ion bombardment, primarily towards the surface, limiting lateral etching. The accuracy of the process can be influenced by numerous parameters such as gas composition, pressure, and RF power. By altering these variables, experts can control the etching process, from the etch rate to the etch profile, optimizing the method for different materials and applications. Thus, RIE offers an exceptional level of control, making it a favored technology for manufacturing intricate micro-devices in the semiconductor industry.
2 Types of Etching
Reactive ion etching (RIE) and isotropic plasma etching are two types of etching processes that are used to remove material from a surface.
The main difference between them is that Reactive Ion Etching is an anysotropic process, i.e. it’s etching capabiltities are not the same in all three spatial directions.
Typically the etching rate in the vertical direction is much higher that the other two. This allows the RIE process to create very precise and deep trenches that are the building blocks of the semiconductor devices.
1. Reactive Ion Etching
RIE is renowned for its precision, predominantly etching in the vertical direction which makes it excellent for creating small, detailed features.
This anisotropic etching — etching that differs in different directions — provides an incredibly high degree of control, allowing for the creation of complex microstructures with minimal damage to the material.
However, this process can be more complex and time-consuming to set up and optimize due to the number of parameters that can be adjusted. In addition, RIE systems tend to be more expensive due to the high-frequency equipment used to generate the ionizing electric field.
2. Isotropic Plasma Etching
Isotropic plasma etching is a type of etching process where the material is removed in all directions.
This process can be used when a big amount of material needs to be removed without the need of creating defined patterns.
For example, when removing photoresist material from a semiconductor device during a Plasma Descum process, it may not be important to remove the photoresist material only in one specific direction as the goal may be to remove it all.
Using an isotropic process may help increase the etch rate and lead to shorter and less expensive processes.
Learn More About Reactive Ion Etching
Overall, Reactive Ion Etching (RIE) is a powerful and precise etching process that uses plasma to remove small amounts of material from a surface. RIE is widely used in high-tech industries, particularly in the production of computer parts like semiconductors, where precision is crucial.
While there are other types of etching processes, RIE is a popular choice due to its directional quality, which makes it ideal for high-tech manufacturing applications. For those looking to learn more about RIE, consulting with the experienced team at SCI Plasma can provide valuable guidance and techniques to meet specific project needs, leading to optimal performance and quality in devices.
Don't hesitate to reach out to SCI Plasma for help and guidance on your Reactive Ion Etching requirements. Their expertise can help take your project to new heights and unlock its full potential.