What Can Plasma Cleaning Do-And Why It's More Than Just a Surface Tidy-Up
- Davide
- 1 day ago
- 4 min read
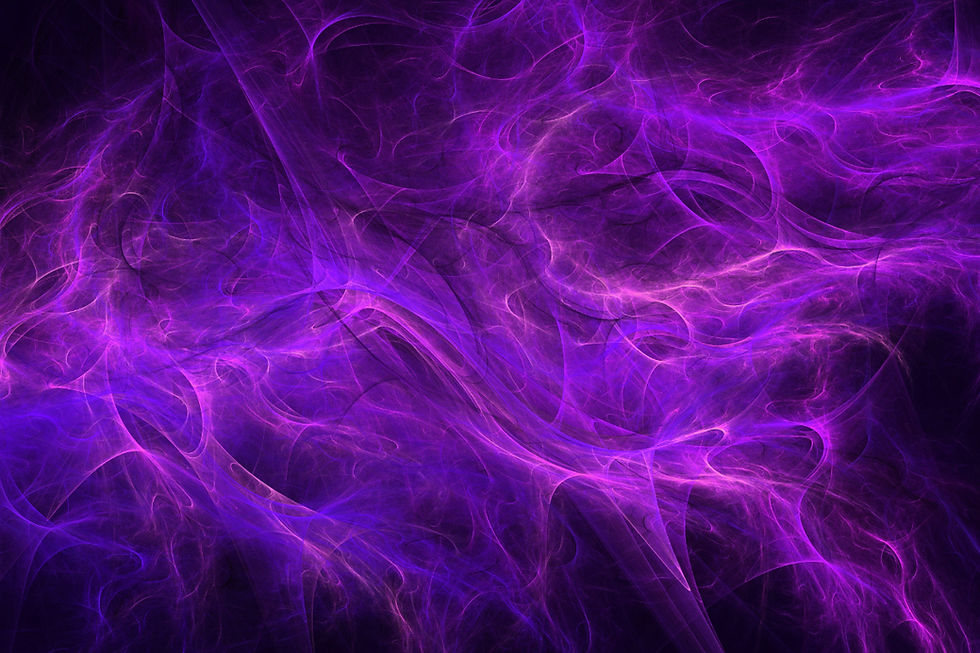
At a glance, plasma cleaning might seem like just another step in the production line—something that removes contamination so you can get on with bonding, moulding, or coating. But there’s far more going on beneath the surface.
Used correctly, plasma cleaning does more than just prepare a surface—it fundamentally improves how your materials interact. It gives you cleaner parts, yes—but also stronger bonds, better yield, and fewer post-process failures.
Here’s what it actually does, how it compares to other cleaning methods, and why timing matters more than you think.
The Hidden Benefit Most People Miss
Most manufacturers know plasma cleaning is good at removing contamination. But what’s less understood is that it also leaves the surface activated—primed for bonding in a way that other cleaning methods can’t replicate.
A. Once contaminants are removed, plasma continues interacting with the clean surface, introducing energy and reactive species
B. These reactive sites create an “activated” surface, which is ideal for bonding and assembly—if used in time
This activation creates temporary surface energy, meaning molecules on the surface are more chemically ‘excited’ and likely to bond. This directly improves the integrity of metallic bonds (such as in wire bonding), polymer adhesion, and other surface-level processes.
However, this effect doesn’t last forever. Activation begins to decay as the surface interacts with air and environmental factors. That’s why timing is critical—bonding or moulding steps should ideally occur within 30 minutes to a few hours of plasma treatment.
How It Works (In Simple Terms)
Plasma cleaning works on two levels—removal and activation—and both rely on physics, not chemicals.
A surface contaminated with organic residues, oxides, or particles enters the plasma chamber
Ionised gas is introduced and energised, creating a mix of electrons, ions, and radicals
These particles collide with the surface, breaking down contaminants at the molecular level
Contaminants are then evacuated, often as vapour or gas, leaving behind a bare, clean surface
At the same time, this process leaves the surface in an “energised” or activated state
This dual-action result—clean and chemically reactive—sets plasma apart from traditional methods. It doesn’t just make the part cleaner. It prepares it for what comes next with scientific precision.
How It Stacks Up Against Other Cleaning Methods
If you’ve been using traditional cleaning methods, you’re not alone. But each method comes with limitations—especially when it comes to consistency and microscopic precision.
• Wet cleaning: Often the first choice in electronics and plastics. It uses solvents or detergents to dissolve contaminants, but can leave behind residues and lacks any surface activation benefits. There's also a growing regulatory burden on chemical waste disposal.
• Laser cleaning: Uses focused light pulses to ablate debris. It can be effective but is limited in surface uniformity, and can damage sensitive materials or introduce heat-affected zones.
• CO₂ cleaning: Fires high-velocity dry ice particles onto the surface, which sublimate and lift contamination. It’s good for dust or particulate removal but not effective at the molecular level.
Plasma, by contrast, works best when you need absolute precision, no chemical residue, and a surface that’s ready to perform. It’s especially useful for bonding, sealing, encapsulating, or coating applications where adhesion quality is non-negotiable.
Do You Always Need a Double Clean?
The short answer: not always. But let’s break it down.
a) When contamination is heavy or greasy, you may need to start with a wet clean to dissolve the bulk of it. Plasma alone would struggle to penetrate deep organic build-up or thick flux.
b) Plasma excels at the final 10%—removing the last microscopic layer and creating surface activation that wet cleaning can’t offer.
This double-clean approach is common in environments where contamination is introduced in multiple process steps—like flux-heavy soldering or certain moulding operations. But for high-spec, tightly controlled production lines, plasma alone is often sufficient.
And that’s important. Because plasma isn’t just a “backup” cleaner—it’s a performance enabler, especially when upstream processes are already clean and controlled.
When You Use It Right, Here’s What You Get
When plasma cleaning is integrated at the right step and used at the right time, it delivers a level of process consistency most manufacturers don’t realise they were missing.
Bond strength improves: Whether you're wire bonding gold to aluminium, or applying a conformal coating, plasma-treated surfaces result in stronger, more uniform adhesion.
Failure rates drop: Especially in environmental stress testing (thermal cycling, vibration, humidity), where good bonding makes or breaks long-term reliability.
Yield stabilises: As processes become more predictable, scrap is reduced and performance shifts from reactive to proactive.
And it’s not just the big numbers that change. Teams notice fewer reworks. QA sees fewer red flags. Customers notice more consistent quality.
This is how surface prep quietly becomes a competitive advantage.
Ready to Rethink Surface Prep?
If you're still relying on outdated cleaning methods—or just treating surface prep as a tick-box exercise—you’re likely leaving performance on the table.
Plasma cleaning doesn’t just clean. It improves outcomes. It stabilises processes. It reduces risk.
And the best part? The change isn’t theoretical. It’s measurable—fewer defects, stronger bonds, and more confidence in every component you ship.
Speak to the SCI Plasma team to evaluate your current surface prep approach and explore how plasma can fit into your production process.
Comentarios